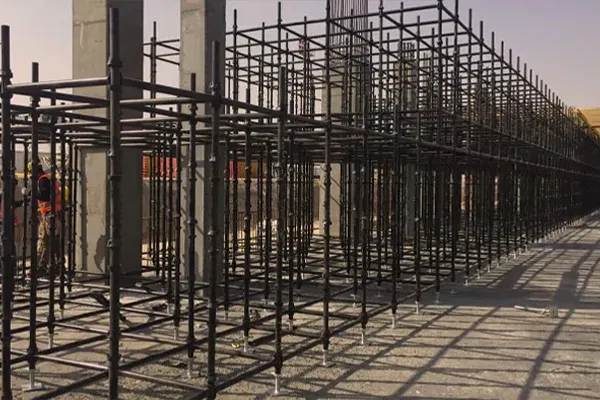
- Published:
- Written by: B.F.S Industries
Cup Lock Scaffolding Installation Manual
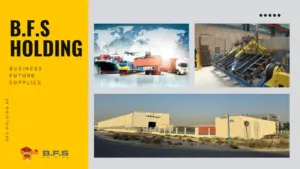
FREE DOWNLOAD – B.F.S. HOLDING
Explore the full spectrum of services and industries covered by B.F.S. Holding.
Cup lock scaffolding, a cornerstone in concrete construction, is a modular system renowned for its efficiency, safety, and versatility in modern construction projects. Engineered by BFS Industries, this system offers a robust solution for shoring and structural support, making it a preferred choice for projects ranging from residential buildings to complex industrial structures. This comprehensive guide provides a step-by-step manual for installing cup lock scaffolding, ensuring safety, efficiency, and compliance with industry standards.
Whether you’re a contractor, engineer, or construction professional, understanding the installation process, components, and safety protocols of cup lock scaffolding is crucial. This article, crafted with insights from BFS Industries, covers everything from the system’s components to maintenance tips, ensuring you have the knowledge to execute a successful setup for shoring and concrete construction projects.
What Is Cup Lock Scaffolding?
Cup lock scaffolding, a cornerstone in concrete construction, is a modular system widely recognized for its efficiency and versatility in construction projects. Designed by BFS Industries, this system features a unique locking mechanism that uses top and bottom cups to secure horizontal ledgers to vertical standards, ensuring a robust and stable structure. Its adaptability makes it ideal for a variety of applications, from residential buildings to large-scale industrial projects, offering unmatched reliability in shoring and structural support.
The cup lock system stands out due to its tool-free assembly and high load-bearing capacity, making it a preferred choice in the construction industry. By enabling rapid setup and dismantling, it reduces labor costs and project timelines. Its widespread use in BFS Industries projects highlights its role in modern construction, particularly in complex designs where safety and stability are paramount.
How It Works and Common Applications
The functionality of cup lock scaffolding lies in its innovative locking mechanism, where a top cup rotates to secure ledgers and verticals, creating a rigid connection without the need for bolts or pins. This design ensures quick assembly, which is critical for time-sensitive projects like concrete construction and shoring tasks. The system’s versatility allows it to support curved, circular, or irregularly shaped structures, making it indispensable for both commercial and industrial applications.
In practice, cup lock scaffolding is used in projects ranging from bridge construction to high-rise buildings. Its ability to handle heavy loads makes it ideal for supporting formwork in concrete construction, while its modular nature suits temporary structures like event stages or maintenance platforms. BFS Industries has leveraged this system in numerous projects, showcasing its reliability across diverse construction environments.
The cup lock scaffolding system, engineered by BFS Industries, is renowned for its modular design and robust components, making it a top choice for concrete construction and shoring projects. Understanding its key parts is essential for safe and efficient assembly, ensuring stability and reliability in demanding construction environments.
This section explores the primary components of cup lock scaffolding, including vertical standards, horizontal ledgers, top and bottom cups, base jacks, sole plates, and diagonal braces. Each element plays a critical role in creating a secure and adaptable structure, ideal for shoring applications and complex concrete construction tasks managed by BFS Industries.
Vertical Standards (Upright Tubes)
Vertical standards, or upright tubes, are the backbone of cup lock scaffolding, providing the primary structural support for concrete construction projects. Crafted from high-strength steel by BFS Industries, these tubes feature fixed bottom cups at regular intervals, allowing secure connections with horizontal ledgers to form a stable framework.
Their robust design ensures high load-bearing capacity, making them essential for shoring applications where heavy loads are common. BFS Industries engineers these standards for durability and precision, ensuring they meet the rigorous demands of modern construction sites.
Horizontal Ledgers (Cross Members)
Horizontal ledgers are the cross members that connect vertical standards, creating the scaffold’s framework in cup lock scaffolding systems. Designed by BFS Industries, these ledgers feature blades at each end that slot into the cups of vertical standards, ensuring a secure and rigid connection for concrete construction tasks.
Their modular design allows flexibility in configuring scaffolds for various project needs, from simple access platforms to complex shoring structures. This ease of installation enhances efficiency, making ledgers a vital component in BFS Industries’ scaffolding solutions.
Top Cup and Bottom Cup (Locking Mechanism)
The top and bottom cups form the innovative locking mechanism of cup lock scaffolding, eliminating the need for tools during assembly. The bottom cup, fixed to the vertical standard, holds the ledger blade, while the top cup rotates to secure it, creating a strong joint for concrete construction projects, as designed by BFS Industries.
This tool-free system enhances construction safety by ensuring quick and secure connections, critical for shoring applications. The durability of these cups, a hallmark of BFS Industries’ engineering, ensures long-term reliability in demanding construction environments.
Base Jacks and Sole Plates
Base jacks and sole plates provide a stable foundation for cup lock scaffolding, essential for concrete construction on uneven surfaces. BFS Industries designs adjustable base jacks to level the scaffold, while sole plates distribute weight to prevent sinking, ensuring stability in shoring tasks.
These components are critical for maintaining structural integrity, particularly in large-scale projects. By adhering to BFS Industries’ guidelines, construction teams can create a secure base, enhancing construction safety and supporting heavy loads in concrete construction applications.
Diagonal Braces (for Additional Stability)
Diagonal braces enhance the stability of cup lock scaffolding by preventing lateral movement, a key feature for concrete construction and shoring projects. BFS Industries designs these braces to integrate seamlessly with the system, connecting vertical standards at an angle to form a rigid, triangulated structure.
Their inclusion is vital for tall or complex scaffolds, ensuring construction safety under heavy loads or adverse conditions. BFS Industries’ diagonal braces are engineered for easy installation, making them indispensable for reliable shoring applications.
Advantages of Cup Lock Scaffolding in Construction
The cup lock scaffolding system offers numerous benefits, making it a top choice for concrete construction and shoring projects. Its tool-free assembly allows workers to set up and dismantle structures quickly, reducing labor costs and project timelines. This efficiency, coupled with the system’s high load-bearing capacity, makes it ideal for supporting heavy formwork or providing access in complex industrial projects managed by BFS Industries.
Additionally, the cup lock system’s modular design enables it to adapt to various project requirements, from simple access platforms to intricate shoring structures. Its secure locking mechanism ensures construction safety, while its versatility supports a wide range of applications, making it a preferred solution for modern construction challenges.
Fast, Strong, and Versatile
The fast assembly of cup lock scaffolding, facilitated by its innovative locking mechanism, significantly reduces construction timelines, a critical factor in time-sensitive projects like concrete construction. The strong and secure joints, engineered by BFS Industries, provide exceptional stability, allowing the system to support heavy loads without compromising safety. This makes it ideal for industrial projects and complex structures.
Its versatility extends to various construction environments, from residential buildings to large-scale infrastructure projects. The ability to configure the system for curved or irregular designs ensures it meets the needs of diverse shoring applications, reinforcing its value in BFS Industries’ portfolio of scaffolding solutions.
Pre-Installation Checklist
Proper preparation is the foundation of a safe and efficient cup lock scaffolding setup, particularly for concrete construction and shoring projects. BFS Industries emphasizes the importance of a thorough pre-installation checklist to ensure scaffold stability and compliance with industry safety standards, minimizing risks and enhancing project success.
This section outlines critical steps to verify site conditions, component integrity, and project requirements before assembling cup lock scaffolding. By following BFS Industries’ guidelines, construction teams can ensure a secure and reliable setup, optimizing construction safety and performance in demanding shoring and concrete construction environments.
What to Check Before Installing Cup Lock Scaffolding
Before installing cup lock scaffolding, a thorough pre-installation checklist is essential to ensure construction safety and efficiency. Start by assessing the site to confirm that the ground is stable and capable of supporting the scaffold’s load, particularly for concrete construction projects. BFS Industries emphasizes the importance of this step to prevent structural failures and ensure compliance with industry standards.
Next, verify that all components, including vertical standards, ledgers, and cups, are in good condition and free from defects. This preparation, combined with a clear understanding of the project’s requirements, ensures that the cup lock scaffolding is installed correctly, providing a safe and reliable platform for shoring and other construction tasks.
Level, Inspect, and Plan
Leveling the ground surface is a critical step to ensure the scaffold’s stability, especially on uneven terrain common in concrete construction sites. Using base jacks and sole plates, workers can achieve a level foundation, as recommended by BFS Industries. Inspecting all components for damage or wear prevents potential failures during assembly, ensuring a secure structure.
Reviewing the project layout and scaffold design is equally important to align the setup with the project’s specific needs. This planning phase, crucial for shoring applications, ensures that the scaffold meets load-bearing capacity requirements and safety standards, setting the stage for a successful installation.
Cup Lock Scaffolding Installation Guide
Installing cup lock scaffolding is a critical process that demands precision and adherence to safety protocols to ensure scaffold stability in concrete construction and shoring projects. BFS Industries provides a streamlined, tool-free system that simplifies assembly while maintaining high standards of construction safety, making it a preferred choice for efficient and secure scaffolding setups.
This section offers a detailed, step-by-step guide to assembling cup lock scaffolding, covering everything from setting up the base to conducting final safety inspections. By following BFS Industries’ proven methods, construction teams can achieve a robust and reliable scaffold structure, optimized for shoring and concrete construction applications.
Step-by-Step Installation Process
Installing cup lock scaffolding requires a systematic approach to ensure construction safety and structural integrity. Begin by setting up base jacks and sole plates on a level surface, providing a stable foundation for the scaffold, particularly for concrete construction projects. BFS Industries recommends precise leveling to prevent tilting or instability during use.
Next, install the first level of vertical standards, connecting them with horizontal ledgers and securing them with the top and bottom cups. This process, repeated for upper levels, ensures a robust structure capable of supporting heavy loads in shoring applications, with each step carefully executed to meet BFS Industries’ safety standards.
Step 1 – Set Up Base Jacks and Sole Plates
The installation begins with placing sole plates on the ground to distribute the scaffold’s weight evenly, followed by adjustable base jacks to achieve a level base. This step is critical for concrete construction projects, where uneven ground can compromise construction safety. BFS Industries designs these components to handle significant loads, ensuring a solid foundation.
Proper alignment and leveling of base jacks prevent structural issues, particularly in shoring tasks where stability is paramount. By following BFS Industries’ guidelines, workers can create a reliable base that supports the entire cup lock scaffolding system, setting the stage for a secure installation.
Step 2 – Install the First Level of Vertical Standards
With the base jacks in place, install the vertical standards by inserting them into the base jacks, ensuring they are plumb and aligned. This step forms the structural backbone of the cup lock scaffolding, critical for concrete construction and shoring applications. BFS Industries’ vertical standards are designed for easy installation and maximum durability.
Securing the first level of verticals correctly ensures that subsequent components, such as ledgers and braces, can be installed without issues. This foundational step is crucial for maintaining the scaffold’s integrity, particularly in demanding BFS Industries projects.
Step 3 – Connect Horizontal Ledgers to the Verticals
Horizontal ledgers are then connected to the vertical standards, forming the scaffold’s framework. The ledger blades slot into the bottom cups of the verticals, creating a stable connection that supports heavy loads in concrete construction. BFS Industries’ ledgers are engineered for precision, ensuring a secure fit without the need for additional tools.
This step enhances the scaffold’s structural integrity, allowing it to support workers and materials safely. The ease of connecting ledgers makes the cup lock scaffolding efficient for shoring tasks, reducing assembly time while maintaining construction safety standards.
Step 4 – Lock the Connections Using Top and Bottom Cups
The top and bottom cups are used to lock the ledger blades to the vertical standards, creating a rigid and secure joint. This tool-free locking mechanism, a hallmark of BFS Industries’ design, ensures quick assembly and disassembly, ideal for concrete construction projects with tight schedules. The cups’ durability ensures long-term reliability.
Proper locking is essential to prevent movement or instability, particularly in shoring applications where heavy loads are common. By following BFS Industries’ guidelines, workers can achieve a secure cup lock scaffolding that meets construction safety and performance requirements.
Step 5 – Repeat for Upper Levels as Required
For multi-level scaffolds, repeat the process of installing vertical standards and horizontal ledgers for each level, ensuring consistent alignment and secure connections. This step is critical for tall structures in concrete construction, where the scaffold must support significant load-bearing capacity. BFS Industries’ modular design simplifies this process, ensuring efficiency.
Each level must be carefully aligned to maintain structural integrity, particularly in shoring applications. Regular checks during this phase ensure that the cup lock scaffolding remains stable and safe, adhering to BFS Industries’ high standards for construction safety.
Step 6 – Add Diagonal Braces for Enhanced Stability
Diagonal braces are installed to enhance the stability of cup lock scaffolding, particularly for tall or complex structures used in concrete construction. These braces, designed by BFS Industries, connect vertical standards at an angle, preventing lateral movement and ensuring a rigid framework. This step is crucial for shoring tasks where stability is critical.
Proper installation of diagonal braces ensures that the scaffold can withstand external forces, such as wind or heavy loads. BFS Industries’ braces are engineered for easy integration, making this step straightforward while significantly improving construction safety.
Step 7 – Perform a Full Structural Safety Inspection
Before use, conduct a thorough safety inspection to verify that all components are securely connected and the scaffold is stable. This step is essential for concrete construction and shoring projects, where construction safety is paramount. BFS Industries recommends checking all joints, braces, and platforms to ensure compliance with safety standards.
A comprehensive inspection identifies any issues, such as loose connections or damaged components, before workers access the scaffold. This final step ensures that the cup lock scaffolding is ready for safe and efficient use in BFS Industries’ projects.
Safety Guidelines During Assembly
Ensuring construction safety during the assembly of cup lock scaffolding is paramount, particularly for concrete construction and shoring projects where structural integrity is critical. BFS Industries emphasizes strict adherence to safety protocols to prevent accidents and maintain scaffold stability, ensuring a secure working environment for construction teams.
This section outlines essential safety guidelines and best practices for assembling cup lock scaffolding, covering load limits, platform requirements, and access protocols. By following BFS Industries’ recommendations, workers can mitigate risks and achieve a safe, efficient setup for shoring and concrete construction applications.
Scaffolding Safety Tips and Best Practices
Construction safety is a top priority when assembling cup lock scaffolding, particularly in concrete construction projects. Adhering to load capacity limits ensures that the scaffold can safely support workers, materials, and equipment. BFS Industries provides clear guidelines on load-bearing capacity, helping prevent overloading and structural failures.
Using proper working platforms, such as planks or decks, ensures a safe working surface for workers. Installing guardrails and toe boards, as recommended by BFS Industries, prevents falls and dropped objects, enhancing safety during shoring and other construction tasks.
Additional Safety Measures
Ensuring safe access and egress is critical for worker safety, with ladders or stair towers providing secure entry and exit points. BFS Industries emphasizes the importance of maintaining clear pathways to prevent accidents during concrete construction projects. Regular safety training for workers further enhances on-site construction safety.
Additionally, regular inspections during assembly ensure that the cup lock scaffolding remains stable and secure. By following BFS Industries’ safety protocols, workers can minimize risks, ensuring a safe and efficient setup for shoring and other construction applications.
Common Installation Mistakes to Avoid
Avoiding common errors during the assembly of cup lock scaffolding is crucial for ensuring construction safety and scaffold stability in concrete construction and shoring projects. BFS Industries highlights that even minor oversights can lead to significant safety risks or project delays, making it essential to understand and address potential pitfalls during installation.
This section identifies the most frequent mistakes made when setting up cup lock scaffolding and provides practical solutions to prevent them. By adhering to BFS Industries’ guidelines, construction teams can achieve a secure and efficient scaffold setup, minimizing risks and optimizing performance for shoring and concrete construction applications.
Top Errors Made During Cup Lock Scaffold Assembly
One common mistake is failing to properly prepare the ground, leading to an uneven base that compromises the scaffold’s stability. This is particularly critical in concrete construction projects, where a level foundation is essential. BFS Industries stresses the importance of using base jacks and sole plates to achieve a stable base.
Another frequent error is using damaged or missing components, which can weaken the cup lock scaffolding structure. Inspecting all parts before assembly, as recommended by BFS Industries, ensures that the system performs reliably in shoring applications, preventing costly delays or safety issues.
Additional Pitfalls to Watch For
Improper locking of joints is another common mistake that can lead to instability, particularly in concrete construction projects. Ensuring that top and bottom cups are correctly engaged, as per BFS Industries’ guidelines, is critical for a secure scaffold. Skipping this step can result in loose connections and safety hazards.
Neglecting structural design considerations, such as load distribution or brace placement, can also compromise the scaffold’s performance. BFS Industries recommends thorough planning and adherence to design specifications to ensure a safe and efficient setup for shoring and other applications.
Comparison with Other Scaffolding Systems
Selecting the right scaffolding system is critical for ensuring construction safety and efficiency in concrete construction and shoring projects, and cup lock scaffolding stands out as a leading choice. BFS Industries has engineered this modular scaffolding system to offer unique advantages, but understanding how it compares to alternatives like ring lock and tube-and-clamp systems helps contractors make informed decisions for their specific project needs.
This section provides a detailed comparison of cup lock scaffolding with other popular scaffolding systems, highlighting their strengths and weaknesses. By exploring these differences, as recommended by BFS Industries, construction professionals can better appreciate why cup lock scaffolding excels in shoring and concrete construction applications, balancing speed, stability, and versatility.
Cup Lock vs. Other Scaffold Types
When comparing cup lock scaffolding to other systems, its unique locking mechanism and versatility stand out. Unlike ring lock systems, which use a rosette design, cup lock scaffolding, developed by BFS Industries, offers faster assembly and greater adaptability for concrete construction projects. Its ability to handle complex geometries makes it ideal for shoring tasks.
In contrast, tube and clamp systems rely on manual connections, which are time-consuming and less secure. Cup lock scaffolding’s tool-free assembly and robust joints provide a significant advantage, particularly in large-scale BFS Industries projects where efficiency and construction safety are critical.
Cup Lock vs. Ring Lock
Cup lock scaffolding excels in speed and ease of assembly compared to ring lock systems, which require more components and connections. While ring lock systems are versatile, cup lock’s simpler design, championed by BFS Industries, makes it ideal for concrete construction and shoring applications where rapid setup is essential.
However, ring lock systems may offer greater flexibility for highly irregular structures. Despite this, cup lock’s high load-bearing capacity and secure joints make it a preferred choice for BFS Industries’ projects, balancing speed, safety, and versatility.
Cup Lock vs. Tube & Clamp
Tube and clamp scaffolding, while flexible, requires skilled labor and more time to assemble than cup lock scaffolding. BFS Industries’ cup lock system eliminates the need for bolts or clamps, streamlining the setup process for concrete construction projects. Its modular design ensures consistent performance across various applications.
The main drawback of tube and clamp systems is their reliance on manual connections, which can lead to inconsistencies. Cup lock’s standardized components and secure locking mechanism make it a more reliable choice for shoring tasks, as endorsed by BFS Industries.
Pros and Cons of Each System
Cup lock scaffolding offers fast assembly, high load-bearing capacity, and versatility, making it ideal for concrete construction and shoring projects. However, it may be less flexible for highly irregular structures compared to ring lock systems. BFS Industries’ cup lock design prioritizes efficiency and construction safety, making it a top choice for most construction needs.
Tube and clamp systems provide flexibility but require more time and skill, while ring lock systems offer versatility at the cost of additional components. For BFS Industries’ projects, cup lock scaffolding strikes the best balance of speed, strength, and adaptability, particularly for shoring applications.
Maintenance Tips for Longevity
Proper maintenance of cup lock scaffolding is essential to ensure scaffold durability and construction safety in concrete construction and shoring projects. BFS Industries emphasizes that regular care extends the lifespan of the system, reducing costs and maintaining reliable performance across demanding construction environments.
This section provides practical tips for maintaining cup lock scaffolding, from cleaning and lubricating components to preventing corrosion and ensuring proper storage. By following BFS Industries’ guidelines, construction teams can maximize the longevity and safety of their scaffolding systems, ensuring optimal functionality for shoring and concrete construction applications.
How to Maintain Cup Lock Scaffolding for Long-Term Use
Regular maintenance is key to ensuring the longevity of cup lock scaffolding, particularly for concrete construction projects. Cleaning and lubricating the locking components, such as top and bottom cups, prevents wear and ensures smooth operation. BFS Industries recommends routine maintenance to maintain the system’s performance.
Preventing rust and corrosion is also critical, especially in humid or coastal environments. Applying protective coatings and storing components in dry conditions, as advised by BFS Industries, extends the lifespan of the scaffold, ensuring it remains reliable for shoring and other applications.
Additional Maintenance Practices
Regular inspections during extended projects help identify wear or damage early, preventing safety issues. BFS Industries suggests checking all components, including vertical standards and ledgers, for signs of stress or corrosion. This proactive approach ensures the cup lock scaffolding remains safe and functional for concrete construction tasks.
Proper storage in dry, secure conditions protects the scaffold from environmental damage. By following BFS Industries’ maintenance guidelines, construction teams can maximize the durability and performance of their cup lock scaffolding, ensuring long-term reliability for shoring projects.
Why Cup Lock Scaffolding Is Ideal for Modern Construction
Cup lock scaffolding, designed by BFS Industries, is a game-changer in concrete construction and shoring due to its speed, strength, and versatility. Its tool-free assembly and secure locking mechanism reduce setup time while ensuring construction safety, making it ideal for a wide range of projects, from residential buildings to industrial complexes. The system’s ability to handle heavy load-bearing capacity and adapt to complex designs sets it apart as a top choice for modern construction.
Its versatility supports diverse project types, while its efficiency saves time and labor costs. By choosing cup lock scaffolding, construction teams can achieve reliable, safe, and cost-effective solutions, as demonstrated by BFS Industries’ successful implementations in shoring and concrete construction projects.
Frequently Asked Questions (FAQs)
1- Is cup lock scaffolding suitable for tall structures?
Yes, cup lock scaffolding, developed by BFS Industries, is ideal for tall structures due to its high load-bearing capacity and secure locking mechanism. When properly installed with diagonal braces, it provides the stability needed for concrete construction and shoring in high-rise projects.
2- How many workers are needed for setup?
The number of workers depends on the project size, but typically, a team of 3-5 workers can efficiently assemble cup lock scaffolding. BFS Industries’ tool-free design simplifies the process, reducing the need for large crews in shoring applications.
3- How long does installation take?
Installation time varies based on the scaffold’s size and complexity, but the cup lock system’s modular design allows for rapid assembly. For a standard setup in concrete construction, BFS Industries estimates 1-2 days for a small to medium structure with a skilled team.
4- Can parts from different manufacturers be mixed?
Mixing parts from different manufacturers is not recommended, as compatibility issues may compromise construction safety and performance. BFS Industries advises using only their components to ensure a secure and reliable cup lock scaffolding system for shoring and concrete construction projects.
Content
Related Posts
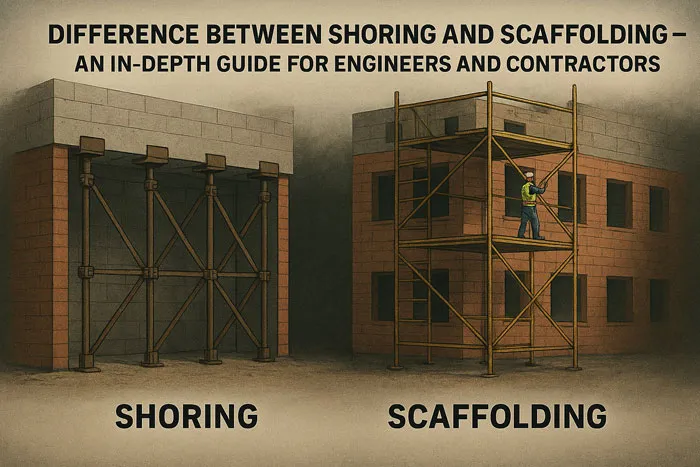