Pipe Rack Design
Introduction
Easy international payment and all official international banks.
Be in touch with our experts at any time of the day or night.
Choose the products you need from B.F.S products
Be aware of discounts by registering on the site in addition to shopping.
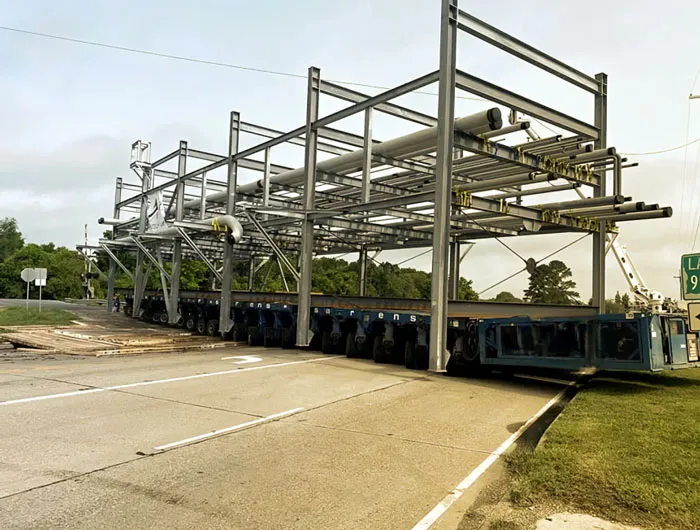
The Importance of Engineering Design in Pipe Racks
The exact and engineered design of industrial pipe racks is of utmost importance. Design engineers create the most efficient structure to support the weight of pipes, cables, and ancillary equipment, as well as loads from wind, earthquakes, and snow, by considering international standards, building codes, and particular project needs. Advanced 3D Building Information Modeling (BIM) software allows precise visualization of the structure, identification of possible interferences, and layout optimization of several components.
Also important during the design phase of the pipe rack structure are concerns of simple access for maintenance, adequate room for the installation of additional pipes, and the likelihood of future facility growth. Modular steel structure design can offer more flexibility throughout building and development stages, hence cutting both time and implementation expenses.
The Role of Materials and Fabrication in Pipe Rack Quality
Careful manufacturing techniques and the choice of premium materials guarantee the long-lasting and safe operation of pipe rack industrials. Especially in industrial settings with severe weather conditions and corrosive chemicals, the use of high-strength steels and protective coatings against corrosion is absolutely vital.
The fabrication process of the steel structure for pipe racks involves precise cutting, component assembly, and welding in accordance with recognized standards. Rigorous quality control at all stages of fabrication, from the selection of raw materials to the final inspection, prevents potential problems during operation. The use of innovative construction methods and prefabricated connections can accelerate the execution speed and improve the final quality.
Advantages of Using Standard and Efficient Pipe Racks
The use of a standard and efficient pipe rack structure offers numerous benefits for various industries, including:
- Organization of Piping and Cabling Systems: Pipe racks let cables and pipes be consolidated and systematically routed, hence reducing complexity, facilitating identification, and improving access.
- Enhanced Safety: Raising pipes and wires above ground level helps to lower the hazards connected with collisions with mobile machinery and people. Access to control tools and valves for maintenance also becomes safer.
- Improved Accessibility for Maintenance: Inspection, maintenance, and pipe, valve, and instrument repair are made easier by the open design of pipe racks. This availability cuts maintenance expenses and lowers downtime.
- Space Optimization: Pipe racks let industrial sites with limited space use vertical space effectively, hence releasing important ground space for other activities and equipment.
- Flexibility and Expandability: A well-designed pipe rack system offers long-term flexibility for the facility by accommodating future expansions and changes to the piping and cabling systems.
- Cost-Effectiveness: Although the first expenditure on a strong steel pipe rack structure is required, the long-term advantages of lower maintenance, enhanced safety, and successful operations help to general cost-effectiveness.
- Environmental Benefits: Pipe racks help to reduce the possibility of leaks and spills by means of a safe and orderly system for moving fluids and gases, hence supporting environmental protection.
Considerations for Pipe Rack Design and Implementation
Several critical factors must be considered during the design and implementation of pipe rack industrials:
- Load Analysis: Accurate calculation of the weight of pipes, fluids, insulation, cables, and potential dynamic loads (wind, seismic) is essential for ensuring the structural integrity of the pipe rack structure.
- Material Selection: Choosing the appropriate grade of steel and protective coatings based on the environmental conditions and the substances being transported is crucial for longevity and corrosion resistance.
- Structural Analysis: Comprehensive structural analysis, including stress, deflection, and stability checks, must be performed to ensure the steel structure can safely withstand all anticipated loads.
- Layout and Spacing: Careful consideration of pipe diameters, insulation requirements, maintenance access, and future expansion needs is necessary for an optimal layout and spacing of the pipe rack.
- Support Design: The design of pipe supports, including shoes, rollers, and spring hangers, must accommodate thermal expansion and contraction of the pipelines to prevent stress on the pipe rack structure.
- Construction and Erection: Employing experienced contractors and adhering to strict quality control procedures during the construction and erection phases are vital for ensuring the integrity and safety of the pipe rack structure.
- Regulatory Compliance: Adherence to relevant industry standards, building codes, and environmental regulations is mandatory throughout the design, construction, and operation of pipe rack industrials.
Advanced Technologies and Innovations in Pipe Racks
Driven by technology developments and the need for more efficiency and safety, the pipe rack industrials area is always changing. The design, building, and maintenance of pipe rack systems is seeing growing use of several creative technologies and ideas.
BIM
The increasing use of sophisticated modeling and simulation tools is one such development. Building Information Modeling (BIM) goes beyond basic 3D modeling to provide complete digital representations of the whole pipe rack structure, including all its parts and their interactions. This allows for more precise cost estimates, enhanced stakeholder cooperation, and better clash detection.
Moreover, by simulating its behavior under several load scenarios, FEA software helps to optimize the steel structure design by guaranteeing structural integrity and reducing material use.
New Materials
Pipe racks’ material utilization is another field of invention. Although steel construction is still the preferred option, developments in high-strength, lightweight steel alloys are providing better strength-to-weight ratios, hence enabling perhaps lighter and more affordable designs. In particular uses where corrosion resistance and non-conductivity are vital, composite materials such as fiber-reinforced polymers (FRP) are also becoming popular. Although these materials may be more expensive, they can be lighter than conventional steel and offer excellent resistance to severe chemical conditions.
Pre-Assembled Modules
Techniques of modular construction and prefabrication are also changing the way pipe racks are built. Construction schedules can be greatly shortened, and the quality of welds and connections can be enhanced by manufacturing major sections of the pipe rack system off-site in regulated settings. Transported to the location and built, these pre-assembled modules minimize on-site disturbance and improve safety. Large-scale projects and those with limited timeframes especially benefit from this strategy.
Monitoring
Smart technologies’ integration is also starting to affect pipe rack management and maintenance. The steel framework can have wireless sensors put on it to track temperature, vibration, and stress, among other things. Structural health monitoring using this information helps to identify any problems early and supports proactive maintenance plans. Digital twins—virtual replicas of the physical pipe rack structure—can combine data from these Sensors and other sources to provide a thorough picture of the system’s performance and enable predictive maintenance, which lowers the operational costs and downtime of pipe rack industries.
Comparison of Common Pipe Rack Materials
Material | Key Advantages | Key Disadvantages | Typical Applications |
Carbon Steel | High strength, cost-effective, readily available, and well-established fabrication | Susceptible to corrosion, requires protective coatings | Most general industrial applications, especially for large and heavy loads |
High-Strength Steel | Higher strength-to-weight ratio, potential for lighter structures | Higher initial cost, may require specialized welding procedures | Applications where weight reduction is critical or for higher load capacities |
Stainless Steel | Excellent corrosion resistance, hygienic | Higher initial cost | Food processing, pharmaceuticals, and chemical plants handling corrosive materials |
FRP (Fiberglass) | Excellent corrosion resistance, lightweight, non-conductive | Higher initial cost, lower stiffness compared to steel, and UV degradation potential | Chemical plants, offshore platforms, and applications requiring electrical insulation |
Reinforced Concrete | High load-bearing capacity, good fire resistance | Bulky, heavy, less flexible for modifications, longer construction time | Large, heavy-duty structures, often used for supporting large diameter pipes |
The Future of Pipe Rack Technology
The field of pipe rack industrials continues to evolve with advancements in materials science, design software, and construction techniques. The increasing adoption of modular design and prefabrication is streamlining construction processes and reducing on-site work. Furthermore, the integration of smart technologies, such as sensors for structural health monitoring and digital twins for predictive maintenance, promises to enhance the safety and efficiency of pipe rack operations in the future. The focus remains on creating robust, cost-effective, and sustainable pipe rack structure solutions that meet the evolving needs of diverse industrial applications. The ongoing innovation in steel structure design and fabrication will further contribute to the optimization of pipe rack industrials for enhanced performance and longevity.
Frequently Asked Questions (FAQ) - Pipe Racks
What is the primary purpose of a pipe rack in an industrial facility?
Pipe racks are primarily used to support and organize piping systems, electrical cables, and instrument pathways, ensuring safe and efficient transportation of fluids, gases, and power throughout the facility.
What materials are commonly used for constructing pipe racks?
The most common material for pipe rack structure construction is steel structure due to its strength, durability, and cost-effectiveness. However, in specific applications, other materials like reinforced concrete or fiberglass-reinforced plastic (FRP) may be used.
What factors influence the design of a pipe rack?
Several factors influence pipe rack design, including the number and size of pipes and cables, the weight of transported materials, environmental loads (wind, seismic, snow), accessibility requirements for maintenance, and future expansion plans.
What are the different types of pipe rack structures?
Common types of pipe rack structures include single-level, multi-level, and pipe bridges. They can be self-supporting or attached to other plant structures, depending on the specific requirements of the facility.
What are the key benefits of using well-designed pipe racks?
Key benefits include improved safety, better organization of utilities, enhanced accessibility for maintenance, optimized space utilization, flexibility for future modifications, and overall cost-effectiveness in the long run.