Double Sided Wall Formwork: The Backbone of Strong Concrete Walls
Introduction
Easy international payment and all official international banks.
Be in touch with our experts at any time of the day or night.
Choose the products you need from B.F.S products
Be aware of discounts by registering on the site in addition to shopping.
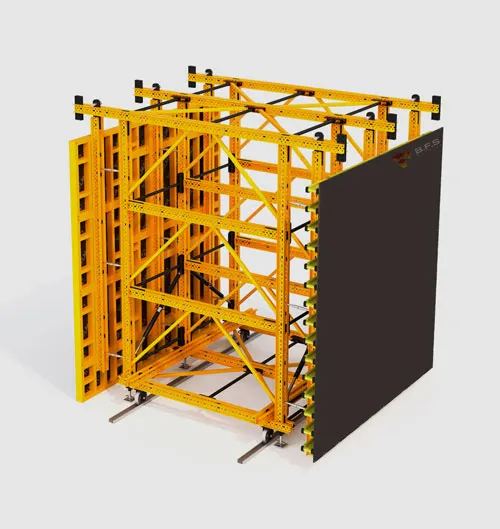
What Is Double Sided Wall Formwork?
Fundamentally, double-sided wall formwork is a technique used in concrete construction to support both sides of the form with an adjustable, structured system in order to mold vertical concrete walls. Double-sided wall systems are freestanding in contrast to single-sided systems, in which only one face of the formwork is supported and the other is dependent on an existing structure, such as soil or a slab. Because of this, they are highly adaptable for a variety of uses, particularly in situations where the wall is being poured in an open area. This flexibility is further enhanced when integrated with Modular Formwork Systems, which allow for quick assembly, easy customization, and repeated use across multiple projects.
Usually, the system consists of two formwork panels placed across from one another with a space for the concrete between them. Steel walers, tie rods, alignment bars, and vertical supports hold these panels in place, guaranteeing structural alignment and consistent wall thickness. A neat, well-formed wall that is prepared for the following phase of construction is revealed when the forms are removed after the concrete has been poured and allowed to cure.
Key Components of a Double Sided Wall System
A properly configured double sided wall system relies on several critical components, each serving a unique purpose in maintaining form alignment, supporting loads, and ensuring safety. Here’s a breakdown of the essential elements:
Component | Function |
Formwork Panels | These are the actual molds where concrete is poured. Usually made of steel or aluminum for durability and reusability. |
Tie Rods | Positioned through both panels to hold them together and maintain consistent wall thickness. |
Walers | Horizontal steel or aluminum beams that help distribute the concrete pressure evenly across the panels. |
Alignment Bars / Braces | Keep the panels vertically aligned during concrete pouring and curing. |
Anchoring System | Ensures stability by securing the formwork to the ground or structural base. |
These elements come together to form a safe, reusable, and highly efficient mold for wall construction. Most systems are modular, making them adaptable for different wall heights and thicknesses.
Why Use Double Sided Wall Formwork?
Now that we’ve covered what it is and how it’s built, let’s talk about why the double sided wall formwork system is a go-to solution for professionals in concrete construction.
1. Strength and Stability
Unlike single-sided systems, which often require an existing surface or backfill to resist concrete pressure, double sided wall systems are completely self-supporting. This makes them ideal for applications like lift shafts, stairwells, tanks, and free-standing walls, where stability and strength are non-negotiable.
2. Speed and Efficiency
Formwork is one of the most time-consuming tasks in wall construction. Double sided systems speed things up by allowing both sides of the wall to be formed and poured at once, reducing labor time and equipment needs. The modular design also makes assembly and disassembly quicker.
3. Accuracy and Finish Quality
Thanks to rigid components like steel panels and tie rods, these systems maintain perfect alignment and create uniform wall thickness. This results in high-quality concrete finishes that often require little to no further treatment or surface correction.
4. Reusability and Cost Savings
Most double sided wall formworks are designed to be reused across multiple projects. This not only saves on material costs but also reduces waste—a big plus for contractors focused on sustainability.
Common Applications of Double Sided Wall Formwork
Double sided wall systems are used across various construction projects—from small-scale buildings to massive infrastructure works. Here are some of the most common applications:
- Basement walls: These walls often need to withstand soil pressure and moisture, making a strong, consistent concrete wall essential. Double sided wall formwork provides that strength with a clean, reinforced build.
- Water tanks and retaining walls: These structures must hold back large volumes of water or soil, which puts stress on both faces of the wall. Using double sided systems ensures structural integrity on both sides.
- Lift shafts and stair cores: In commercial and residential high-rises, elevator shafts and stairwells are usually among the first vertical elements constructed. Double sided formwork helps build them quickly and accurately.
- Tunnels and bridges: In civil engineering, formwork systems that provide high load resistance and fast cycle times are crucial. Double sided wall formworks meet those demands effectively.
Whether you’re building a multi-storey apartment or an industrial-grade facility, the versatility of this system makes it a reliable tool in nearly all vertical concrete construction.
How to Set Up Double Sided Wall Formwork: Key Tips
Proper setup of double sided wall formwork is essential to ensuring safety, accuracy, and speed on-site. Here are some professional tips and best practices:
- Plan according to the pour height and wall thickness: Different wall dimensions require different types and strengths of formwork panels, tie rods, and supports.
- Check the alignment continuously: Misalignment can cause uneven walls and stress concentrations. Use laser levels or plumb bobs to make sure your setup is vertically accurate.
- Install tie rods at the correct spacing: Too few tie rods can result in panel bulging or even blowouts during pouring. Refer to manufacturer’s guidelines for spacing and tension requirements.
- Lubricate the formwork panels before pouring: A release agent ensures that panels don’t stick to cured concrete, making removal easier and extending the lifespan of your equipment.
- Use safety platforms and scaffolding where necessary: For high walls, proper access and fall protection are critical.
- Disassemble carefully: After curing, remove panels in reverse order and inspect components for wear before reuse.
By following these steps, your crew can reduce errors, minimize rework, and keep the job site safer and more efficient.
Pros and Cons of Double Sided Wall Systems
Every system has its strengths and limitations. Here’s a quick comparison to help you evaluate if double sided wall formwork is right for your project:
Pros | Cons |
Supports high wall heights and thicknesses | Requires more space around the wall for installation |
Ensures high dimensional accuracy | Initial setup can be time-consuming |
Offers excellent concrete finish quality | Heavier than single-sided systems; may need lifting gear |
Reusable across multiple projects | Requires training for proper use and safety |
Suitable for free-standing and exposed wall applications | May involve higher upfront costs |
For projects that demand quality, reusability, and long-term cost-efficiency, the advantages clearly outweigh the drawbacks.
Choosing the Right Double Sided Wall Formwork for Your Project
Selecting the right double sided wall system depends on several critical project-specific factors. Not all formwork is created equal, and making the right choice can save both time and money.
Start by considering wall dimensions. For taller or thicker walls, you’ll need a robust formwork system with stronger tie rods and braces to withstand concrete pressure. In contrast, smaller projects may benefit from lightweight aluminum systems that are easier to handle and quicker to set up.
Next, think about reusability and project duration. If you’re managing a long-term or multi-phase build, investing in higher-quality, reusable wall formworks will pay off over time. On shorter or one-off jobs, rental options may be more cost-effective.
Also, evaluate site access and space. Some formwork systems need room on both sides of the wall for setup and bracing, which may not be feasible on tight job sites or urban construction zones.
Lastly, factor in crew experience. Complex systems may require more training or skilled labor. The right formwork should match your team’s capabilities while meeting engineering and safety standards.
Choosing wisely ensures your concrete construction process is smooth, efficient, and structurally sound from start to finish.
Final Thoughts: Why Double Sided Wall Formwork Matters
At a glance, formwork may just seem like a temporary step in concrete construction. But in reality, it plays a huge role in the speed, safety, and outcome of a project. Double sided wall formwork not only helps deliver structurally sound walls but also streamlines the entire building process.
From the modular double sided wall system to the clever design of tie rods and braces, this setup embodies the balance between function, flexibility, and finish quality. For any team looking to scale concrete walls with efficiency and precision, this system is a no-brainer
Frequently Asked Questions (FAQs)
1. What is the difference between single-sided and double sided wall formwork?
Single-sided formwork supports only one face of the wall and is usually used when the other side has backfill or an existing structure. Double sided formwork supports both faces, making it suitable for free-standing walls or where access to both sides is available.
2. Is double sided wall formwork reusable?
Yes. Most systems are designed for multiple reuses, especially those made from steel or aluminum. With proper maintenance and storage, they can last for years.
3. Can I use double sided wall systems for curved walls?
Specialized versions of double sided formwork systems can be adjusted or fabricated to create curved wall sections, but standard systems are primarily used for straight walls.
4. What factors determine the choice of wall formworks?
Wall height, thickness, concrete pressure, site conditions, budget, and speed requirements all influence the type of formwork you should use.
5. How long should I wait to remove the formwork after pouring concrete?
This depends on temperature, humidity, and concrete type. Typically, formwork can be removed after 24–48 hours for standard concrete, but always follow your structural engineer’s recommendations.