Bolt and Nut Steel Structures
Introduction
Easy international payment and all official international banks.
Be in touch with our experts at any time of the day or night.
Choose the products you need from B.F.S products
Be aware of discounts by registering on the site in addition to shopping.
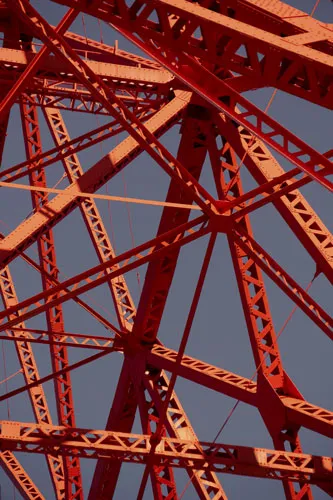
The Rise of Bolt and Nut Systems in Construction
As construction timelines shorten and safety standards increase, bolt and nut steel structures have emerged as a practical and efficient solution. They reduce on-site labor, minimize error, and offer enhanced control during both the manufacturing and installation phases. These benefits are especially valuable in fast-paced industries such as logistics, oil & gas, and infrastructure development, where delays can significantly impact project costs and stakeholder satisfaction.
The rapid advancement of materials science and fabrication technology has further strengthened the case for bolted steel systems. Companies like BFS Industries are at the forefront of this innovation, delivering engineered steel solutions that combine precision, durability, and speed. Their work in optimizing splice connection systems has helped reduce overall project costs while maintaining structural integrity. By incorporating sophisticated modeling and testing, BFS ensures that each connection meets rigorous performance standards in both static and dynamic load conditions
Key Components of a Bolt and Nut Steel Structure
A bolt and nut steel structure typically consists of vertical columns, horizontal beams, bracing systems, and various types of connection plates. These components are pre-manufactured in controlled factory environments to ensure precision and uniformity. Once delivered to the construction site, they are assembled using high-tensile bolts that meet strict engineering standards, often involving torque-controlled tightening for maximum performance.
The joints in these structures play a critical role in distributing loads and maintaining the system’s integrity under stress. Unlike welded joints, which can suffer from thermal distortion and site-dependent variability, bolted joints offer consistent performance. The modular nature of these components also facilitates rapid assembly and simplifies maintenance over time. This modularity allows engineers to make design modifications without extensive structural rework, contributing to more efficient life-cycle management of buildings and infrastructure.
Main Advantages of Bolted Steel Structures
Speed is one of the most significant advantages of using bolt and nut steel structures. Prefabricated components are delivered ready for installation, significantly reducing on-site work. This streamlined process is particularly useful in urban environments where time, space, and disruption must be minimized. Bolted systems also eliminate the need for complex site preparation, enabling construction to proceed even in challenging environments.
In terms of quality, bolted connections provide uniform performance, especially when fabricated and installed by experienced teams like those at BFS Industries. These structures also offer superior earthquake resistance due to their ability to absorb and redistribute dynamic forces more effectively than welded joints. In addition, bolted systems perform well under high-temperature conditions, offering better fire resistance compared to welded structures, which may fail more rapidly under thermal stress.
Types of Bolts Used in Steel Structures
Steel structures use a variety of bolts, each designed for specific load types and environmental conditions. Common types include ordinary bolts, precision bolts, and high-strength bolts. Among high-strength bolts, there are friction-type and bearing-type categories, depending on how the load is transferred through the joint. Friction-type bolts use surface tension to resist movement, while bearing-type bolts allow some slip before locking in under pressure.
Additional fasteners include large hexagonal bolts, torsional shear bolts, and anchor bolts. In advanced applications, chemical anchors and expansion bolts may also be used. Each type serves a specific structural need, especially in high-load areas like splice connection zones, where stability and alignment are critical. Selection of the correct bolt type is essential for structural integrity, and depends on factors like load direction, vibration exposure, and thermal expansion.
Manufacturing and Installation Process
The manufacturing process begins with cutting and drilling steel plates to precise dimensions based on detailed engineering drawings. These components are then assembled in modules at the factory, ensuring quality control at every step. Pre-assembly reduces waste and improves safety by moving labor-intensive processes away from the construction site. Advanced fabrication lines also include automated welding robots for auxiliary connections and CNC machines for high-precision drilling.
Installation on-site involves lifting preassembled segments and securing them with bolts according to a pre-planned layout. Skilled crews check alignment, torque settings, and joint integrity throughout the process. This modular approach minimizes disruption and allows for parallel workstreams, further accelerating project timelines. Efficient logistics and crane scheduling are essential to maintain workflow and prevent delays during installation.
Bolted vs Welded Structures: A Practical Comparison
Welded structures require skilled labor and longer on-site working hours, which increases costs and risks. In contrast, bolted structures offer a cleaner, safer, and faster alternative. Bolted connections eliminate the need for on-site welding, reducing fire hazards and weather dependencies. They are also less affected by temperature variations, which can compromise weld quality in outdoor environments.
From a maintenance standpoint, bolted structures are easier to inspect and replace if needed. Welds, once completed, are difficult to alter without heavy equipment and potential structural compromise. The flexibility and accessibility of bolted joints make them preferable in many commercial and industrial applications. They also support a more sustainable construction model, as bolts can be reused or replaced without demolishing entire sections of the structure.
Applications of Bolt and Nut Steel Structures
Bolt and nut steel structures are widely used across various industries. Their flexibility and strength make them ideal for warehouses, factories, shopping malls, stadiums, and transportation hubs. In infrastructure projects, they support large-span roofs, mezzanine floors, and even bridge elements. Their high load-bearing capacity and seismic resistance make them particularly valuable in earthquake-prone regions.
These structures are also used in oil refineries, power plants, and logistic centers due to their resistance to harsh environmental conditions. The ability to customize and scale makes them suitable for both temporary and permanent installations, offering long-term value and structural reliability. Their modular design allows for phased construction, enabling clients to adapt and grow operations without full structural overhauls.
Why Choose BFS Industries for Steel Structure Projects?
BFS Industries has extensive experience in delivering high-quality steel structure solutions tailored to client needs. With a strong focus on engineering excellence and timely execution, BFS Industries has become a trusted partner for both local and international projects. Their expertise in bolt and nut systems ensures long-lasting performance and compliance with global standards.
Moreover, BFS Industries excels in advanced joint systems such as splice connection design, ensuring seamless load transfer and structural coherence. Their integrated approach to project planning, fabrication, and assembly results in efficient and economical solutions for complex construction challenges. BFS emphasizes client satisfaction by providing end-to-end support—from design optimization to on-site supervision and post-installation services.
Conclusion
Bolt and nut steel structures represent the future of modern construction—fast, flexible, and reliable. From design to execution, these systems offer unmatched benefits in terms of performance, safety, and cost-efficiency. Their growing adoption across sectors is a testament to their effectiveness in addressing today’s engineering challenges. These structures are not just a trend, but a foundation for sustainable, scalable growth in industrial and commercial development.
If you’re looking for a partner to deliver high-quality bolt and nut steel structures, consider working with BFS Industries. Contact us today to learn more about our services, request a consultation, or get a custom quote for your next project. Let us help you build stronger, smarter, and faster.
Frequently Asked Questions (FAQ)
What is the main benefit of using bolt and nut connections over welding?
Bolt and nut connections offer faster installation, better quality control, and easier maintenance. They eliminate the need for on-site welding, which reduces fire hazards and labor costs. Additionally, bolted joints can be inspected and replaced without damaging the surrounding structure, providing greater long-term flexibility.
Are bolted steel structures suitable for high-rise buildings?
Yes, bolt and nut steel structures are commonly used in high-rise construction due to their strength, modularity, and seismic performance. Their capacity to withstand dynamic loads and facilitate phased construction makes them an excellent choice for vertical structures.
How are bolted joints inspected for safety?
Bolted joints are inspected using torque wrenches, visual checks, and sometimes ultrasonic testing. Preload values are monitored to ensure that the bolts have been tightened correctly. BFS Industries follows strict quality assurance protocols during both fabrication and assembly phases.
Can bolted structures be relocated or reused?
Yes. One of the key advantages of bolt and nut structures is their reusability. Components can be disassembled and relocated with minimal effort, making them ideal for temporary or modular buildings. This not only saves time and money but also supports environmentally sustainable construction practices.
What industries benefit most from bolt and nut steel structures?
Industries such as logistics, energy, manufacturing, aviation, and public infrastructure greatly benefit from bolted structures. Their ability to handle heavy loads, endure harsh conditions, and adapt to different functional needs makes them suitable for a wide variety of applications.